Australia’s Bartle Frere Bananas is piloting RFID technology to track batches of the fruit as they are harvested and shipped to customers, while Internet of Things sensors track moisture and nitrates to protect the Great Barrier Reef.
Jan 10, 2022 Bartle Frere Bananas, located in Queensland, Australia, is using cellular and radio frequency identification (RFID)-based Internet of Things (IoT) technologies to ensure the sustainability of its farm, as well as to improve transparency. The solution, provided by Hitachi Vantara, applies artificial intelligence (AI) to data captured from sensors and RFID tags, in order to manage conditions around the banana plantation (or paddock) and throughout the supply chain.
At Bartle Frere Bananas, IoT sensor data tracks moisture and nitrate levels, while RFID tags on banana bunches monitor their care, harvesting, sorting and shipment. The goal is to improve productivity, says Gavin Devaney, the company’s owner and managing director, while reducing costs and minimizing its environmental footprint. Cat M1 cellular IoT technology provides the data to the cloud, while UHF RFID tags are being read by handheld readers.
The 30-year-old family-run banana producer has spanned multiple generations. The company produces approximately 250,000 15-kilo cartons of fruit annually, 60 percent of which is provided to Aldi supermarkets. The rest of the fruit is split between Woolworths, Coles and an open market where resellers buy fruit for green grocers or independent grocery stores. The farm is located near Australia’s Great Barrier Reef, which is vulnerable to pollutants that could run off from agricultural sites.
Bartle Frere Bananas has a mission of growing its fruit sustainably, the company explains, and to protect the local environment around it, including the reef. In that effort, it participated in a federally funded program known as the Australian Government National Landcare Program, and it also received funding from Hort Innovation to track conditions on its farm by measuring nitrates and soil moisture around its plants. The company then took another step by launching an RFID pilot to track the fruit throughout the supply chain. All of the collected data is managed by Hitchi’s Lumada Manufacturing Insights software.
The deployment began with implementing IoT sensor technology at the plantation. Bartle Frere Bananas contacted Hitachi Vantara in early 2020 to install drainage sensors that could monitor nitrates in the sediment draining from the site, as part of the federal government and industry grant program for data-driven smart farming. The nitrate sensors track not only drainage, but also the use of fertilizer at each section of the plantation. The solar-powered sensors employ edge computing to monitor and report on the amount of nitrate coming through the operations’ draining pipes via a river system that drains into the ocean.
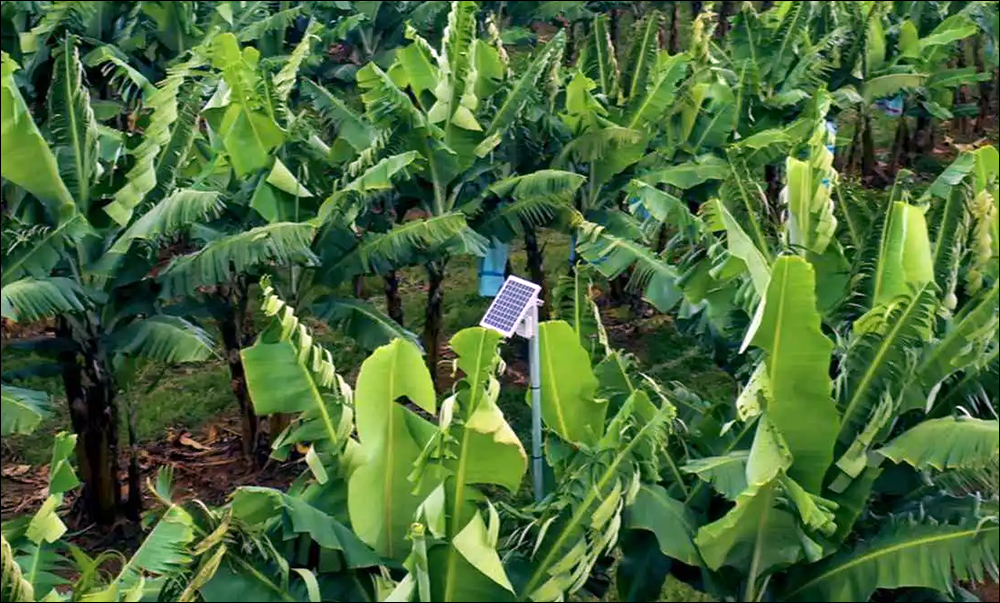
Hitachi installed IoT sensors at the farm to help the company improve its productivity and efficiency.
The system includes moisture sensors to detect irrigation levels, along with when more watering may be required and if there’s a risk of over-watering. Up to six sensors are wired to a gateway node, which forwards the data to the software via a Cat M1 cellular connection. At present, the system informs Bartle Frere Bananas when to turn on the irrigation system, though the actual control of the watering will eventually be automated, according to Owen Keates, a manufacturing practice industry executive at Hitachi Vantara’.
When it comes to managing nitrates, Devaney says, Bartle Frere Bananas is minimizing this contaminant by providing crops with the ideal amount of fertilizer required. “The data is already showing that our practices are working,” he reports. The Lumada Manufacturing Insights software employs AI modelling and analytics to predict when bananas will reach maturity, reduce the number of pesticides that will drift from the intended targets and determine the ideal amount of water to use. Devaney can watch a monitor and access the software to obtain a real-time view of the conditions on the farm, along with recommendations.
Next, the company began examining the supply chain. Typically, green bananas are picked and gas-ripened to ensure they are properly fresh and ripe when they reach stores. “From harvesting to selling,” Devaney reports, “you want it to be as fresh as possible. Controlling that is critical and challenging.” For one thing, he says, bananas have a limited amount of storage time, and the longer they spend in the supply chain or at a distribution center, the less fresh they will be at a store.
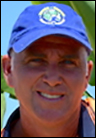
Gavin Devaney
Temperature excursions outside of an optimal window of 14 to 16 degrees Celsius (57 to 61 degrees Fahrenheit) can compromise the bananas’ quality. “You want to manage that process very carefully,” Devaney explains, “so the fruit that people buy is as fresh as possible.” Without RFID or other technologies, he says, the company had to trust the supply chain process once bananas left its premises. Devaney saw an opportunity for RFID to reduce the challenges around fresh fruit delivery to stores, while providing more information to the customers who consume the bananas.
The company sought transparency and traceability from plantation to plate, thereby boosting consumer confidence. Transparency can help customers access Bartle Frere Bananas’ products, Devaney says. “Not too long ago,” he notes, “there was a man who bought bananas in Aldi.” This customer was impressed by their taste and freshness, and he asked the store’s management where the bananas had come from. Once he learned the source of the fruit, he called Bartle Frere Bananas to complement its products and asked how he can be sure to buy them in the future. “People say, ‘I’d like to buy your bananas, but I can’t tell which bananas are yours.’ We want them to know.”
So far, the RFID system has been used as part of a pilot. It starts at the banana plant, where the farm wants to track the chemical treatments provided at each site, then link that data with each banana bunch as it moves toward the store. A passive UHF RFID tag with a unique ID number encoded on it is attached to a bag that is placed over the bunch prior to harvest. That bag encloses the bananas in their own off-gassing, which facilitates the ripening process.
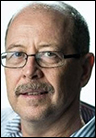
Owen Keates
Employees use handheld readers to interrogate each bunch’s tag ID, and the GPS-based location is linked to those bananas in the software. The tag ID can be linked to other details as well, such as the fertilizer applied to that plant, as well as irrigation readings at that part of the plantation. When the bananas are harvested, the tag is again read to create a date for that event in the software. Then, the tag is interrogated once more as it is sorted and packed in cartons. The ID number, Keates says, is linked to a temperature-controlled container used to transport the fruit to the distribution center.
Bananas can travel 2,000 kilometers (1,243 miles) to Sydney, or 3,000 kilometers (1,864 miles) to Adelaide, in South Australia. To manage conditions, Bartle Frere Bananas is applying IoT devices with GPS trackers, LTE connectivity and temperature sensors, provided by Hitachi Vantara, in refrigerated containers. When connectivity is available, the devices transmit an update about the temperature levels every 30 minutes, and all data is uploaded when the devices reach the DC.
Hitachi Vantara has been providing smart agriculture solutions for years, Keates says, starting in Japan. Its technology was first deployed in Australia for cattle farmers. It helped to digitize the farm, providing insights to farmers about how much water and pasture are available, while tracking the movements of cattle. The company has been working with the National Landcare Program to assist farmers in creating smart, sustainable farms. In the future, it hopes to work with Bartle Frere Bananas to further track its products, by putting RFID tags on labels that could be affixed to each carton and then be tracked all the way to a supermarket.
The collected data provides food-safety integrity, Keates says, so that if the fruit is found to have a problem—when it reaches a store, for instance—the farm could easily trace that batch of product back to its origins. The information culled from an RFID tag could also prove the bananas’ integrity, so the fruit can be sold as a premium-grade product, rather than at a discount. As the food moves from plant to market to consumer, he adds, the tags provide data to validate that each banana was produced to high environmental standards.
In the long term, the goal is paddock-to-plate tracking and transparency, Devaney says, which will support consumer confidence. “I want to get the trials finalized so we can do what we are doing consistently and well,” he states. “Eventually, I want to try and get the marketing giants to see that this sort of stuff can work all the way through, like it has done in the beef industry.”
Devaney has a vision that someone out shopping at a grocery store will eventually be able to scan a QR code on a banana and determine the family farm from which it came. This information could be made available via data captured by RFID and IoT technologies. Scanning a QR could bring a customer to Bartle Frere Bananas’ website. “You could see our website, watch a video, give feedback,” he explains, “and you could get information about how that banana was grown.”